Galvanic corrosion is a chemical and physical phenomenon that affects metals and their alloys when they come in contact with an electrolyte and are electrically connected to a different metal. This type of corrosion is of particular relevance in materials engineering, metalwork preservation, and many industrial and marine applications. To fully understand galvanic corrosion, it is necessary to explore its mechanisms, causes, consequences, and prevention strategies.
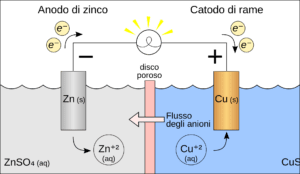
Table of Contents
ToggleThe Mechanisms
Galvanic corrosion occurs when two dissimilar metals, or metal alloys, are placed in electrical contact in the presence of an electrolyte, which can be a conducting liquid such as saline water. The metals involved have different electrochemical potentials. In this galvanic pair, the metal with the most negative potential becomes the anode and oxidizes, giving up electrons, while the metal with the most positive potential acts as the cathode and receives electrons.
The anode undergoes gradual dissolution, with loss of material, while the cathode generally remains intact or may even be protected from galvanic reaction. The rate at which galvanic corrosion occurs depends on the potential difference between the two metals, the conductivity of the electrolyte, and the resistance of the overall electrical circuit.
Some Metals Commonly Subjected
- Steel
- Iron
- Copper
- Aluminum
- Zinc
Factors Influencing Galvanic Corrosion.
Several factors influence the rate and intensity of galvanic corrosion, including:
- Nature of metals: The difference in the standard electrode potentials of the metals involved is crucial. The greater the difference, the greater the risk of accelerated corrosion of the anode.
- Metal area: If the area of the anode is small compared to that of the cathode, corrosion proceeds more rapidly because of the higher current density at the anode.
- Electrolyte conditions: Temperature, salt concentration, pH, and the presence of oxygen affect the conductivity of the electrolyte and thus the rate of corrosion.
- Distance between metals: A smaller distance between metals in a galvanic pair can increase the corrosion rate due to reduced electrical path resistance.
Corrosion Prevention and Counteraction
- Material selection and compatible design
- Cathodic protection (expendable anodes)
- Protective coatings and paints
- Periodic inspection and maintenance
Chemical Nickel Plating as a Solution to Electrolytic Corrosion
- Formation of a protective barrier
- Nickel coating properties (e.g., uniformity, corrosion resistance)
- Typical applications (electronic components, automotive parts)
- Learn more about the process of Chemical Nickel Plating
Learn more about each form of corrosion on Wikipedia