La nichelatura chimica, conosciuta anche come electroless nickel plating, è un processo di deposizione del nichel che non richiede corrente elettrica. A differenza della galvanostegia, che utilizza un flusso di elettroni per ridurre gli ioni metallici sulla superficie di un substrato, la nichelatura chimica sfrutta una reazione chimica autonoma. Questo metodo permette di ottenere un rivestimento uniforme, anche su geometrie complesse, ed è ampiamente utilizzato per componenti industriali di alta precisione, nei settori automobilistico, aerospaziale, elettronico e medicale. Alla base di questo processo vi è la presenza di agenti riducenti, sostanze chimiche che svolgono un ruolo cruciale nella deposizione del nichel, influenzando le proprietà meccaniche e chimiche del rivestimento finale.
Cosa Sono gli Agenti Riducenti?
Gli agenti riducenti sono sostanze chimiche capaci di cedere elettroni durante una reazione di ossidoriduzione. Questo processo consente la riduzione di una specie chimica da uno stato ossidato a uno stato ridotto, favorendo reazioni essenziali in numerosi settori industriali, tra cui quello della nichelatura chimica.
Nel contesto della nichelatura chimica, gli agenti riducenti hanno il compito di trasformare gli ioni di nichel (Ni²⁺) presenti in soluzione in nichel metallico (Ni⁰), favorendo la deposizione di uno strato uniforme sul substrato.
Meccanismo della Reazione Chimica
Il processo di nichelatura chimica avviene in un bagno chimico, contenente:
- Ioni di nichel (Ni²⁺), derivanti da un sale solubile di nichel
- Agenti riducenti, che forniscono gli elettroni necessari alla riduzione
- Stabilizzanti e catalizzatori, che regolano la reazione e ne ottimizzano l’efficienza
Quando l’agente riducente interagisce con gli ioni di nichel, avviene una reazione di ossidoriduzione che converte il nichel in forma metallica, depositandolo sulla superficie del substrato. Il risultato è un rivestimento uniforme e aderente, con caratteristiche variabili a seconda dell’agente riducente utilizzato.
Tipologie di Agenti Riducenti e il Loro Impatto sul Rivestimento
La scelta dell’agente riducente è un fattore determinante nella qualità del rivestimento ottenuto con la nichelatura chimica. Ogni agente riducente influisce in modo significativo sulle proprietà del deposito, tra cui:
- Durezza, che può variare a seconda della composizione chimica e dei trattamenti termici successivi
- Resistenza alla corrosione, fondamentale per applicazioni in ambienti aggressivi o esposti a sostanze chimiche
- Struttura e uniformità dello strato depositato, che determina l’adesione e l’omogeneità del rivestimento su superfici complesse
- Conduttività elettrica, essenziale per applicazioni nel settore elettronico e dell’ingegneria elettrica
Diverse sostanze chimiche possono fungere da agenti riducenti nella nichelatura chimica, ognuna con proprietà e applicazioni specifiche. La loro scelta dipende dai requisiti prestazionali del rivestimento finale, nonché dalle condizioni operative a cui sarà sottoposto.
Ipofosfito di Sodio (NaH₂PO₂)
L’ipofosfito di sodio è l’agente riducente più comune nella nichelatura chimica. La sua reazione genera un rivestimento costituito da nichel e fosforo, la cui composizione varia in base alla concentrazione dell’agente riducente nel bagno.
Caratteristiche principali:
- Produce uno strato contenente tra il 2% e il 14% di fosforo
- Maggiore contenuto di fosforo → maggiore resistenza alla corrosione, ma minore durezza
- Minore contenuto di fosforo → maggiore durezza, ma minore resistenza alla corrosione
- Adatto a geometrie complesse grazie alla deposizione uniforme
Reazione chimica:
Ni²⁺ + H₂PO₂⁻ + H₂O → Ni + H₂PO₃⁻ + 2H⁺
Boridrazina (N₂H₄BH₃) e Dimetilamina Borano (DMAB)
Questi agenti riducenti sono utilizzati per ottenere rivestimenti nichel-boro, che si distinguono dai rivestimenti nichel-fosforo per alcune proprietà uniche.
Caratteristiche principali:
- Offrono una maggiore durezza rispetto al nichel-fosforo
- Possiedono una buona resistenza termica
- Sono meno resistenti alla corrosione rispetto ai rivestimenti ad alto contenuto di fosforo
Reazione chimica:
Ni²⁺ + N₂H₄BH₃ + H₂O → Ni + N₂ + H₃BO₃ + H₂
Idrazina (N₂H₄)
L’idrazina è un agente riducente meno comune, utilizzato in processi specializzati che richiedono rivestimenti di nichel puro, senza la presenza di fosforo o boro.
Caratteristiche principali:
- Crea uno strato di nichel puro, con eccellente conducibilità elettrica
- Meno stabile rispetto agli altri agenti riducenti
- Richiede un controllo rigoroso delle condizioni del bagno
Reazione chimica:
Ni²⁺ + N₂H₄ → Ni + N₂ + 4H⁺
Effetti degli Agenti Riducenti sulle Proprietà del Rivestimento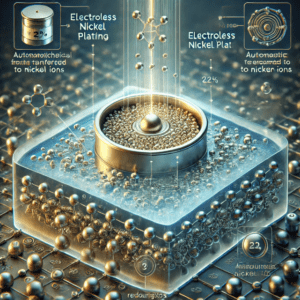
La scelta dell’agente riducente ha un impatto diretto sulle caratteristiche finali del rivestimento, influenzando non solo le proprietà meccaniche, ma anche la durabilità e l’efficienza del materiale nelle applicazioni specifiche.
- Durezza: Il nichel-fosforo basso (con <5% di fosforo) è particolarmente apprezzato per la sua elevata durezza iniziale (~500 HV), che può aumentare con il trattamento termico, mentre il nichel-fosforo alto (con >10% di fosforo) mostra una durezza inferiore (~300 HV), ma offre maggior duttilità e resistenza alla corrosione. Il nichel-boro è il più duro dei tre, raggiungendo valori fino a 1000 HV con il trattamento termico, ma con minor resistenza alla corrosione rispetto al nichel-fosforo alto.
- Resistenza alla Corrosione: Il nichel-fosforo alto è ideale per applicazioni in ambienti chimicamente aggressivi, grazie alla sua eccellente resistenza alla corrosione, mentre il nichel-boro ha una resistenza inferiore. Il nichel puro, ottenuto con l’idrazina, ha una buona resistenza alla corrosione, ma meno efficace rispetto ai rivestimenti ad alto contenuto di fosforo.
- Conducibilità Elettrica: Il nichel puro offre la migliore conducibilità elettrica, rendendolo la scelta ideale per applicazioni elettroniche. Al contrario, il nichel-fosforo presenta una conducibilità più bassa, che peggiora ulteriormente con l’aumento del contenuto di fosforo.
La scelta di un determinato agente riducente deve quindi essere ponderata in base alle necessità specifiche di durezza, resistenza alla corrosione e conducibilità, per ottimizzare le prestazioni del rivestimento nel lungo periodo.
Applicazioni della Nichelatura Chimica
Grazie alla versatilità degli agenti riducenti e alle eccellenti proprietà del rivestimento, la nichelatura chimica trova impiego in numerosi settori industriali, dove le sue caratteristiche migliorano le prestazioni dei componenti.
- Industria automobilistica → protegge componenti come ingranaggi, valvole, cilindri da usura, abrasione e corrosione, estendendo la durata dei veicoli e migliorando l’efficienza dei motori.
- Elettronica → applicata a connettori, circuiti stampati e componenti elettronici per ottimizzare la conducibilità elettrica, affidabilità e resistenza agli shock termici.
- Aerospaziale → impiegata su parti di motori, strutture di aerei e attrezzature satellitari, dove i rivestimenti resistenti all’usura e alle alte temperature migliorano le prestazioni e la sicurezza in ambienti estremi.
- Settore medico → utilizzata per rivestire strumenti chirurgici e impianti biocompatibili (come protesi e stent), per garantire biocompatibilità, resistenza alla corrosione e longevità.
L’adozione della nichelatura chimica in questi settori è cruciale per soddisfare le crescenti esigenze di prestazioni, affidabilità e sicurezza in ambienti estremi e condizioni operative critiche.
Conclusione
Gli agenti riducenti sono fondamentali nel processo di nichelatura chimica, poiché influenzano direttamente le caratteristiche meccaniche e chimiche del rivestimento. La scelta dell’agente riducente più adatto deve considerare le specifiche esigenze dell’applicazione, bilanciando in modo ottimale durezza, resistenza alla corrosione e conducibilità elettrica.
Con l’avanzamento delle tecnologie e la continua ricerca, la nichelatura chimica sta introducendo innovazioni nelle formulazioni degli agenti riducenti, migliorando le prestazioni e l’efficienza dei rivestimenti. Questo processo sta acquisendo sempre più importanza in vari settori industriali, come automobilistico, aerospaziale, elettronico e medico, confermandosi come una tecnologia indispensabile per rispondere alle esigenze moderne di qualità, durata e precisione nelle applicazioni.